SchahlLED Lighting realised the conversion of the lighting to smart LED technology for the agricultural machinery manufacturer Fendt. The company now saves over one million kilowatt hours of electricity per year and has improved the quality of light at the same time.
SchahlLED Lighting has converted six halls of the tractor factory from conventional T5 fluorescent tubes to state-of-the-art LED technology for Fendt. Within just four weeks, 2,000 old lights were dismantled and disposed of and 1,000 new high-performance LED spotlights including a digital control system were put into operation.
When retrofitting six production halls in Marktoberdorf, Bavaria, the renowned tractor and agricultural machinery manufacturer Fendt consistently focussed on efficient technology to increase profitability.
Fendt's requirements for the new lighting were complex: the conversion had to be completed within the four-week shutdown period, the entire system had to be fully programmed by the time it was commissioned and had to have already undergone an effectiveness check. At the same time, the acceptance of the lighting quality by the workforce was tested. "It all had to happen simultaneously," says SchahlLED Managing Director Erich Obermeier.
SchahlLED developed customised solutions to meet all of the customer's specifications, for example for the suspension of the new high bay spotlights: SchahlLED had special steel cables manufactured so that the old 6.5 kilometre long track system could continue to be used. Thanks to the optimised suspension across all spatial axes, a perfect glare-free appearance is now achieved - an important factor for Fendt.
LED lights from Thorlux-Lighting are now being used - like SchahlLED, the company is part of the group of companies owned by British lighting manufacturer FW Thorpe Plc. The new Thorlux lights at Fendt were installed, programmed and commissioned section by section. This meant that the quality and function checks were carried out while other areas were still being refitted. Thanks to the smart lighting control system, all lights are networked with each other via sensors and radio modules, they react to movement and dim down promptly when work is not being carried out in individual areas. The luminaires also dim down automatically when sunlight enters - this prevents overlighting and saves energy.
Fendt now saves a good one million kilowatt hours of electricity per year just by retrofitting the tractor factory, although the light intensity has been increased from 300 to 400 lux to at least 500 lux and in some cases up to 1,000 lux. Fendt had additional high-quality measurement technology installed in advance of the LED conversion to ensure full effectiveness control. Thanks to a subsidy from the Federal Office of Economics and Export Control (BAFA) amounting to 15 per cent of the investment volume, the investment in the new lighting system pays for itself very quickly.
Fendt is convinced by the lights and wants to continue investing in the future. The next step will be to replace around 750 lights in the administration offices and more than 1,000 lights in other areas of the plant. SchahlLED had already converted other halls at Fendt to intelligently controlled LED lights the year before. The old lighting technology dated back to 2012, when LED technology was still in its infancy. However, the efficiency of LED lights has tripled in recent years and the price has halved. "Time to act and convert the remaining halls and company areas," says Fendt.
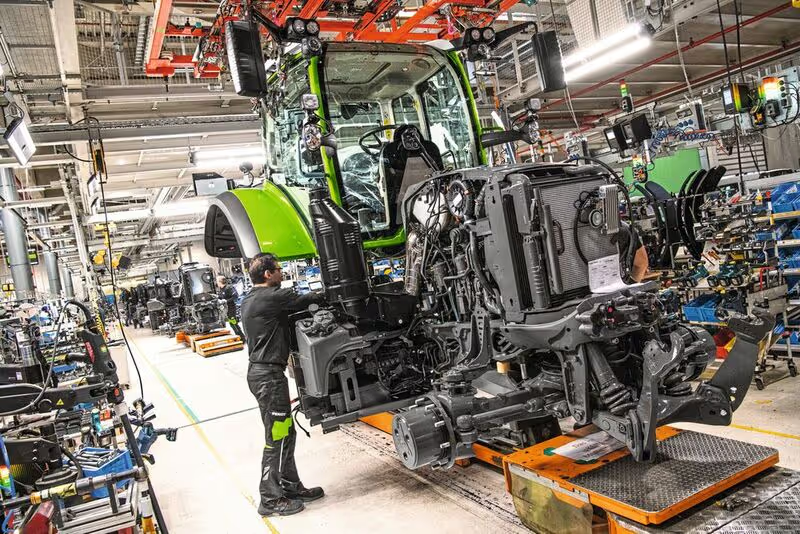
The waiting area of Memmingen Airport.
Data at a glanse:
Reductions / amortisation
CO2-emissions p.a. (kg)
> 70%
Electricity consumption p.a.
> 70%
TCO (Total Cost of Ownership)
>70%
Payback period
approx. 1 year
Reductions / amortisation